Multiaxials: Non-Crimp Fabrics
Innovative and tailor-made: SAERTEX composite reinforcements made of glass, carbon, flax, basalt and aramid fibers. Those materials are also known as NCFs (non-crimp fabrics). We deliver non-crimp fabrics with more than 3,333 article designs. Depending on the fiber type, surface weight and angle combination, various mechanical characteristics can be achieved. SAERTEX multiaxials are individually configured for our customers and optimally adapted to a range of processes in composites manufacturing. Suitable methods are vacuum infusion, RTM, pultrusion, prepreg, compression, etc.
In comparison with crimped fibers, as found in woven textiles for instance, straight lay-up fibers have the greatest possible load-bearing capacity. Composite components manufactured from non-crimp fabrics (NCFs) permit the ideal transmission to the component of the generated forces – in the direction of loading – by specifically adjusting the fibre orientation.
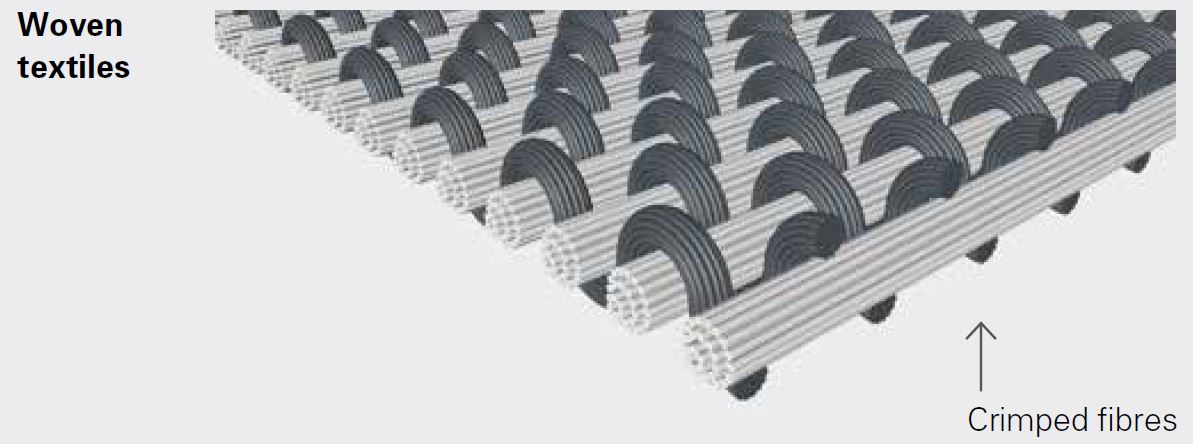
In comparison with standard reinforcement textiles this delivers either reduced component weight for identical mechanical characteristic values, or a higher component loading for the same component weight.